In the realm of electronics manufacturing, the assembly of printed circuit boards (PCBs) is a critical step that determines the functionality and reliability of the final product. Your ability to ensure the quality of PCB Assemblies (PCBA) is directly linked to the testing methods employed after the assembly process. As such, automation has become an integral part of modern PCBA testing, providing a robust framework to catch defects, verify functionality, and uphold high standards of quality and also maintain traceability.
Automated testing serves as a key component in the PCB assembly line, replacing manual inspection with precision and consistency powered by automation. By leveraging state-of-the-art technologies such as IoT integrated with probe tester based jigs and automated inspection systems, you can scrutinize every aspect of a PCBA, from solder connections to component placement without human error. This transition to using automated systems empowers you to handle larger volumes of boards and detect issues that might be invisible to the naked eye.
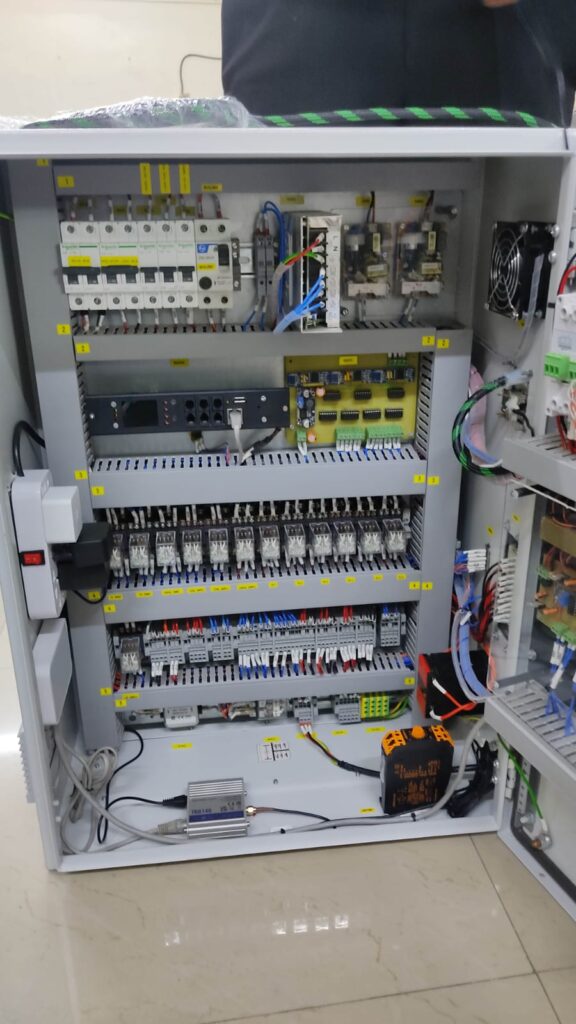
Quality in PCB assembly is non-negotiable, and automated testing ensures that you meet the requisite standards. The integration of automated testing in your manufacturing process allows for real-time feedback and data-driven insights, leading to a streamlined workflow and enhanced productivity. With such systems, diagnosing and rectifying defects become a more manageable task, ensuring that the PCBAs you produce adhere to the highest levels of performance demanded by the industry.
Overview of PCB Assembly Testing
In printed circuit board assembly (PCBA), testing is a critical step that determines the integrity and functionality of the final product. Your understanding of the various testing methods and the role of automation can enhance quality control and efficiency.
Importance of Testing in PCBA
Testing in PCBA is your safeguard against potential defects and ensures that each board meets the requisite electrical standards. It’s a comprehensive quality control process that helps you to identify manufacturing issues such as solder defects, missing components, and incorrect placements (to name a few) early in the production cycle. Automated testing, in particular, provides you with consistent and reliable results, minimizing human error and speeding up the review process.
Types of PCB Assembly Tests
You will encounter several types of PCBA tests, each with unique purposes and methodologies. The most common ones include:
- Automated Optical Inspection (AOI): This test uses high-resolution cameras to scrutinize solder connections and verify component placement and orientation without human intervention.
- In-Circuit Testing (ICT): ICT utilizes specialized fixtures and probes to test the electrical performance of individual components on the board.
- Functional Testing: After assembly, this test simulates the normal operating conditions to check the board’s functionality comprehensively.
Each method is crucial in different stages of the assembly process to ensure the highest standards of product quality.
Evolution of Test Automation
The trajectory of test automation within PCBA has seen significant advancements, moving from manual inspection to highly sophisticated automatic systems. Advancements in technology have paved the way for intricate tests to be conducted swiftly and accurately. High-speed automation not only streamlines the evaluation of electric components but also allows you to analyze large volumes of boards with impressive precision. This evolution culminates in a robust system that can adapt to complex board designs and varied testing requirements, all while maintaining the highest quality standards.
In-Circuit Testing (ICT)
In-circuit testing represents a cornerstone technology in ensuring the quality and functionality of Printed Circuit Board Assembly (PCBA). You’ll find thorough examinations from basic principles to the sophisticated equipment involved, alongside an evaluation of the advantages and constraints tied to the ICT process.
Basics of ICT
In-circuit Testing (ICT) is a form of electrical testing where you check a printed circuit board assembly (PCBA) for shorts, opens, resistance, capacitance, and other basic quantities to confirm the proper assembly of components onto a PCB. ICT operates by accessing test points on a PCB using probes and typically requires a custom “bed-of-nails” test fixture which makes contact with these points to conduct the test.
Key ICT Components:
- Test Points: Strategic points on a PCB used to measure electrical properties.
- Components: Various elements such as capacitors and resistors whose values are verified during ICT.
ICT Equipment and Fixtures
The in-circuit tester is a comprehensive and complex piece of machinery that functions within a test automation framework to evaluate fully populated PCBs. At the heart of ICT lies the “bed-of-nails” tester, which is a dedicated fixture consisting of numerous spring-loaded pins that connect to test points on the board. The design and build of this fixture are specific to the PCB being tested to ensure every component is accurately vetted.
Fixture Details:
- Custom-designed for each PCB
- Contains numerous pins to access test points
Benefits and Limitations of ICT
ICT offers a high level of accuracy in detecting a range of defects such as incorrect component values, polarity issues, and soldering problems. This makes it an invaluable step in the test-process handling, which aims to catch errors before boards proceed to functional testing or are shipped to customers.
Advantages:
- Thorough inspection for various types of potential defects
- Automated, which reduces the likelihood of human error
However, the limitations of ICT lie in the costly and time-consuming fixture fabrication. Further, it might be less effective for complex boards with limited access to test points or for components that require dynamic functional test strategies.
Limitations:
- High initial cost for fixture development
- May not cover all possible board defects, especially for very complex circuits
Automated Optical Inspection (AOI)
As you delve into the world of Printed Circuit Board (PCB) assembly, understanding the critical role of Automated Optical Inspection (AOI) in maintaining quality is essential. AOI systems utilize machine vision to detect a range of defects, which ensures the integrity and functionality of your PCBs.
AOI in Quality Assurance
AOI is your first line of defense in identifying and addressing defects that can compromise PCB quality. These systems are designed to detect:
- Soldering issues: such as insufficient, excessive, or missing solder, and solder bridges.
- Component placement errors: including incorrect components, misaligned or upside-down parts.
- Missing components: ensuring each piece is where it should be.
By integrating AOI in your manufacturing process, you contribute substantially to the overall quality assurance of PCB assembly.
Machine Vision and AOI Systems
Your AOI system is powered by machine vision technology, with high-resolution cameras and sophisticated algorithms to inspect the PCBs. Machine vision in AOI involves:
- Image capture: Cameras take multiple images of the PCB under test.
- Analysis: Software algorithms compare the images to detailed parameters of what a correct PCB should look like.
This process helps in identifying variances, such as component defects or soldering errors, with precision and speed that manual inspection can hardly match.
Optimizing AOI for Better Results
To maximize the benefits of AOI, you want to optimize the process for better results:
- Ensure high-quality images: Proper lighting and camera calibration are key.
- Regular updates: Keep the software updated with the latest inspection parameters.
- Feedback loop: Implement a system where AOI output is used to continually improve the PCB assembly process.
By refining these elements, you heighten the effectiveness of your AOI systems—guaranteeing that you catch more defects earlier in the assembly process.
Functional Testing in PCBA
Functional testing in Printed Circuit Board Assembly (PCBA) is a crucial step in ensuring that each board performs according to its design requirements. This process involves verifying the functionality of the assembled PCB by applying specific tests that simulate real-world conditions.
Functional Test Procedures
Your functional tests should systematically stimulate the PCB’s inputs to mimic its operational environment. Firmware is often loaded onto the board to interface with memories or peripherals and execute the test sequences. The following steps are typically followed:
- Setup: Power the PCBA and configure the required initial conditions.
- Input Stimulation: Apply test signals to the board’s inputs.
- Output Monitoring: Check the corresponding outputs against expected results to determine if the board is functioning correctly.
Configuring Functional Test Fixtures
To carry out functional testing, you’ll need a test fixture that interfaces with your PCBA. Configuring the fixture involves:
- Fixture Design: Tailor the fixture to your board’s specific connectors or test probe points.
- Test Environment: Ensure that the fixture can replicate the PCB’s final electrical environment.
- Loading Essential Software: Install the necessary firmware onto the PCBA, which will interact with the test fixture to conduct the evaluation.
Evaluating PCBA Functional Performance
A successful functional test confirms that all aspects of the PCBA’s functionality meet the intended design specifications. Evaluate your PCBA’s functionality by considering:
- Firmware Interaction: All firmware should communicate effectively with the board’s memory and peripherals.
- Response to Stimuli: Inputs and outputs should correlate accurately under test conditions.
- Final Verification: Confirm that the board’s functionality aligns with the required performance for its real-world application.
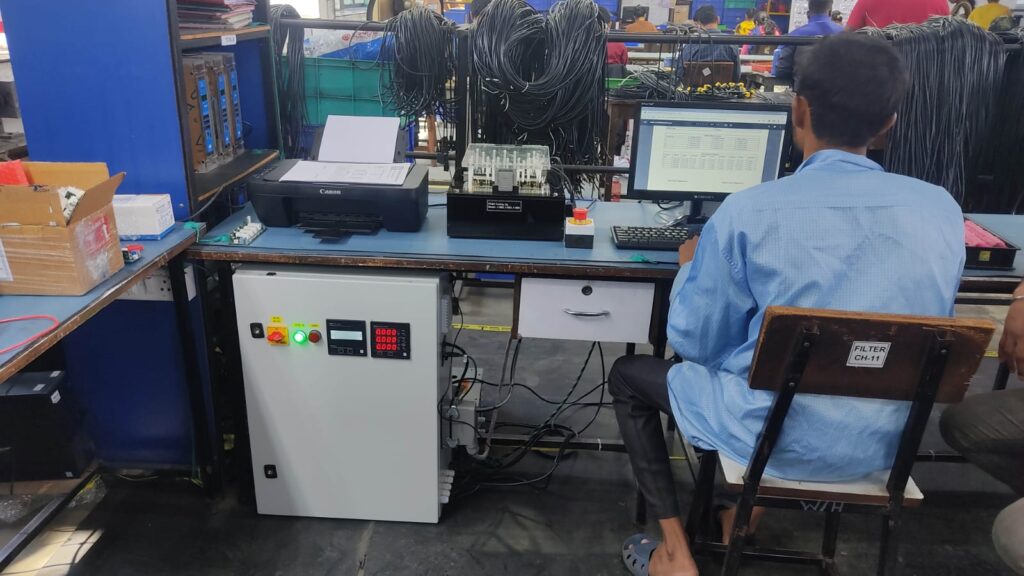
Advanced Testing Techniques
When you are dealing with the complexities of Printed Circuit Board Assembly (PCBA), advanced testing techniques provide accuracy and efficiency in identifying faults. These methodologies have evolved to meet the challenges presented by modern electronic circuits’ interdependencies and density.
Flying Probe and Other Modular Testing
Flying probe testing is a versatile and non-destructive testing method that’s critical for your modern PCBA needs. It uses movable test probes to swiftly check the electrical performance of each component on the board, effectively adapting to various board layouts without the need for a dedicated fixture. Modular testing systems ebb this flexibility, allowing for a customized test setup that can include a range of test and measurement instruments, such as signal generators and digital multimeters programmed using Standard Commands for Programmable Instruments (SCPI). This setup supports easy reconfiguration and scaling to match the electronic circuit complexity you’re dealing with.
Here’s how you might typically structure a flying probe testing system:
- Test Probes: Position these to access circuit nodes.
- Control Software: Uses SCPI for programming instrument’s sequences.
- Measurement Units: Capture the data for analysis.
Data-Driven Fault Analysis
The data-driven fault analysis method utilizes sophisticated algorithms to sift through test data and identify patterns that could indicate potential faults. This analysis is deeply integrated with fault identification systems, ensuring that you are not just collecting data but also interpreting it to improve the manufacturing process. When you apply data-driven fault analysis, it zeroes in on the anomalies and peculiarities that might escape basic inspection, thus enhancing the reliability of your PCBAs.
Adapting to Electronic Circuit Complexity
Your electronics are becoming more intricate, with components like Ball Grid Array (BGA) that pose unique testing challenges due to their hidden solder joints. Adapting to this complexity means leveraging advanced test strategies that understand the interdependency of various electronic components on a PCB. The test systems you set up must be robust enough to not only test individual components but also ensure they function correctly within the circuit’s ecosystem. Integrating comprehensive test and measurement instruments—often controlled via SCPI with precise programming—ensures that complex assemblies are thoroughly vetted for faults.
Remember, the effectiveness of your testing hinges on the interplay between hardware capabilities and the sophistication of your analysis software.
Test Process Optimization
In the fast-evolving electronics industry, streamlining the test process for printed circuit board assembly (PCBA) is crucial for maintaining high-quality standards and reducing costs. By leveraging test automation frameworks and employing thorough test coverage, you can significantly enhance the reliability of PCBAs while keeping manufacturing expenses in check.
Test Automation Frameworks and Tools
Your adoption of test automation frameworks is vital for efficiency. These frameworks offer structured guidelines and tools for automating the testing process, improving code re-usability, portability, and decreasing script support cost. When selecting tools, prioritize those that offer high interchangeability and reduced interdependency to streamline your workflow.
- Guidelines for Automation:
- Code Re-usability: Ensure your automation scripts can be used across different test scenarios.
- Portability: Choose tools that enable testing across various environments and conditions.
- Tool Considerations:
- Interchangeability: Can the tool be adapted for various PCB designs and functions?
- Interdependency: Minimize tools that require extensive interlinking with others, reducing complexity.
Quality and Reliability Through Test Coverage
High test coverage is indicative of the quality and reliability of your PCBAs. It ensures that all functional aspects of the circuit are examined and that potential faults are identified prior to mass production. Good coverage involves not only testing for common scenarios but also accounting for edge cases that could lead to component failures.
- Coverage Goals:
- Comprehensive: Test all functionalities, even the least frequently used ones.
- Edge Cases: Include scenarios that are outside normal operating parameters to enhance reliability.
Reducing Manufacturing Cost with Efficient Testing
Efficient testing methods are pivotal for minimizing manufacturing costs. By identifying and resolving defects early in the manufacturing process through targeted test automation, you can avoid costly reworks and delays. The cost savings from reduced failures also extend to lower warranty claims and improved product lifespan.
- Cost Efficiency Strategies:
- Early Fault Identification: Detect and address issues as early as possible in the manufacturing cycle.
- Streamlined Reworks: Implement efficient testing to decrease the need for expensive reworks and scrap.
By focusing on these strategies, you can optimize the test process for increased quality, reliability, and cost-effectiveness in the assembly of printed circuit boards.
Emerging Trends and Challenges in PCBA Testing
As you navigate the intricacies of Printed Circuit Board Assembly (PCBA) testing, you will encounter a dynamic landscape shaped by technological advancement and the demand for efficiency. Remain cognizant of key industry shifts towards intelligent testing methods and the challenges of implementing sophisticated fault analysis systems.
Cloud connected Test Jigs using IoT
The integration of Internet of Things (IoT) in PCBA testing has led to the development of cloud-connected test jigs. Such test jigs allow for continuous data collection and analysis, providing real-time feedback on the assembly process. They facilitate remote query of test results and adjustments to testing protocols, thereby enhancing the process control and interchangeability of test setups across different facilities.
Test Automation in Industry Evolution
Automation plays a pivotal role in industry evolution, particularly in PCBA testing. Automated test frameworks enable rapid fault detection and functional verification, which are crucial for high-volume production. Your understanding of these systems’ characteristics ensures efficient implementation processes and sustains high yield rates.
Overcoming Test and Measurement Challenges
The complexity of modern PCBAs poses significant challenges in testing and measurement. You must address issues like false positives in fault analysis and the need for adaptable test coverage due to component variability. Employing intelligent test software that learns and adapts to new fault patterns is essential for accurate fault diagnosis.
Future Directions in Automation
Looking forward, anticipate further integration of machine learning and predictive analytics into PCBA testing. Innovations are likely to offer more advanced fault analysis and proactive maintenance capabilities, transforming the landscape of PCBA testing to be more predictive than reactive. Your active engagement with these technologies will be key to their successful implementation.
Conclusions
In the realm of printed circuit board assembly (PCBA), automated testing has emerged as a cornerstone for ensuring product quality and reliability. Your understanding of automated circuit board testing systems is crucial, as they provide a safeguard against potential component failures, many of which can occur during both the assembly process and functional testing stages.
- You have seen that implementing a well-structured Design for Test (DFT) approach is influential in achieving comprehensive PCB test coverage. This serves to ease the testing process and reduce the possibility of overlooking faults.
- Your recognition of automated testing systems, such as the flying probe test system, is essential for their ability to perform intricate verifications without the need for a dedicated test fixture.
It is crucial for you to note that standardized commands, specifically SCPI (Standard Commands for Programmable Instruments), play a pivotal role in the automation of test processes. This standardization aids in efficient configuration and querying during testing, enhancing the reproducibility of test scenarios.
Your awareness of the critical factors in the solder paste printing process—pressure, blade angle, and speed—is strategically significant. They directly influence the yield performance of PCBA, with improvements in these parameters leading to considerable enhancements in yield and efficiency within smart manufacturing environments.
In summary, you should integrate these automated testing solutions into the manufacturing process to reinforce the overall integrity and reliability of the PCBA manufacturing process. This integration not only optimizes quality but also contributes to the economic efficiency of production lines.
For all your needs to Automate PCBA Testing feel free to reach out to us for a hassle-free analysis of your system. We will be here to support you end to end – From initial consulting all the way to system implementation and data analysis.
Email us : info@axonet-emsys.com for your next Automated PCBA Testing experience !